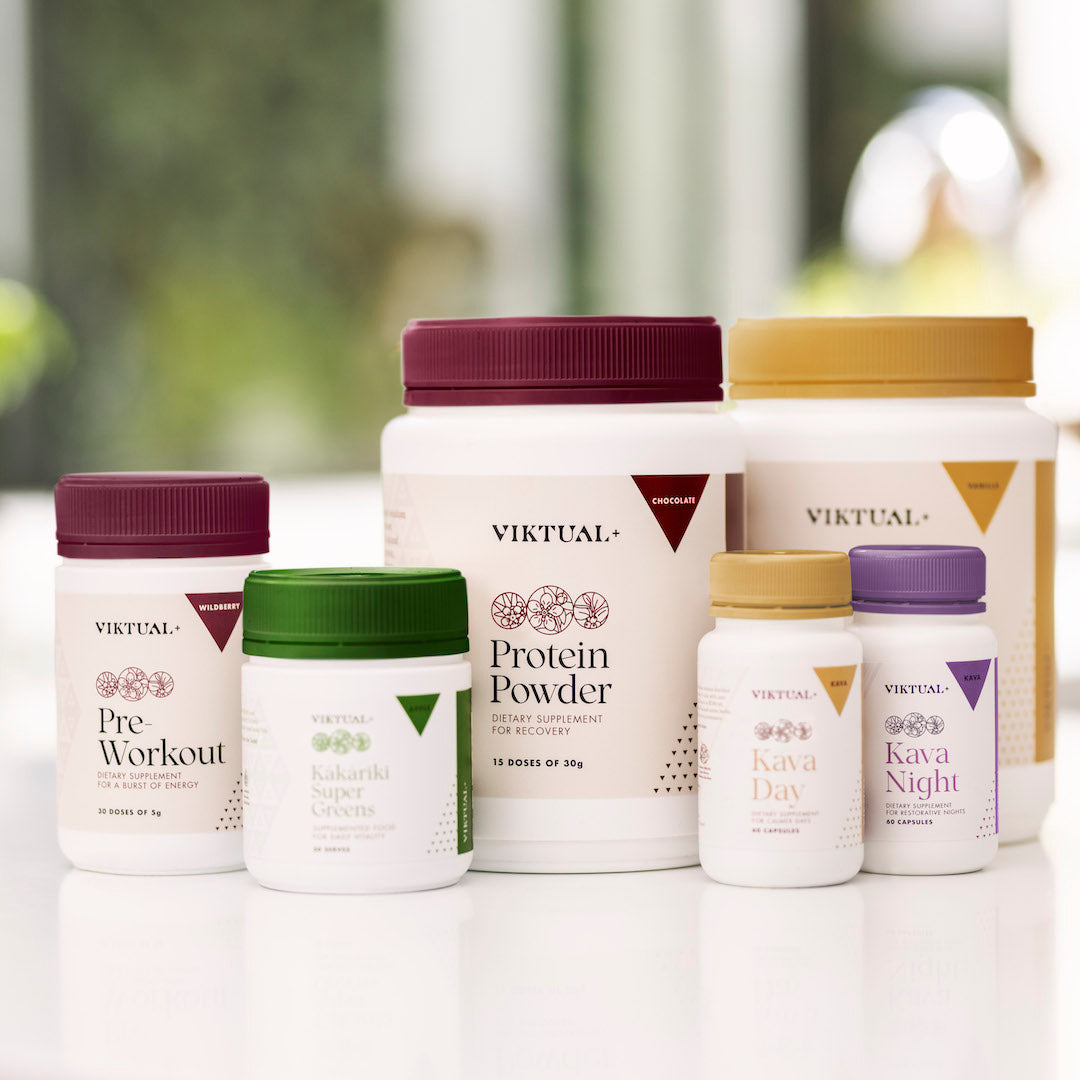
Sustainability Goals – Recyclable containers, Compostable and Biodegradable packaging
When deciding on the packaging of our products, we were met with difficult decision-making. There’s a lot of confusion in regard to home composts vs commercial composting and the effect biodegradables have on landfill environments. Other factors we took into consideration included the shelf-life and tamper evidence capabilities. We have selected recyclable containers, and like Pharmapac (our recyclable container manufacturers), we’re keeping up to date with research and advancements in sustainable packaging.
Some of our most eye-opening learnings were:
- compostable and biodegradable packaging cannot be put into soft plastic or kerbside recycling bins as they’re not designed to be processed by recycling facilities that deal with all other plastics
- if disposed to landfill, biodegradable plastic is likely to produce methane, a known greenhouse gas
- majority of kiwis do not have access to systems that collect and process biodegradable plastics properly
- if biodegradable plastic is left to break down in a natural environment, eg landfills or the sea, it often breaks down into micro-plastics which can create ‘plastic smog’ in the ocean and accumulate in soils
- most compostable plastics are designed to break down in a commercial compost and may not break down in a natural environment
- Nearly all home composts do not reach the required temperature to break down compostable packaging.
Pharmapac have chosen to promote recyclable packaging while they keep up with research and keep an eye on advancements in this area. They’ve also designed features with end recyclability in mind, with all empty containers (when placed in recycle bins) being collected by local councils, recycled and turned into the likes of fence posts by Future Post or office recycling bins by Method Bins.
Life cycle of our containers and lids:
- Our HDPE (High Density Polyethylene) containers and PP (Polypropylene) lids are manufactured in Auckland by Pharmapac which is New Zealand’s only packaging manufacturer to be at the highest environmental level of Toitū Enviromark diamond certified (which is above ISO:14001), 9001:2015 accredited and are a partner of Operation Clean Sweep.
- Once our containers are empty and put into recycling bins, they’re collected at all council kerbside recycling centres or at council recycling centres and are either exported or recycled locally through local reprocesses like Future Post.
- Our PP lids are mostly sorted and recycled locally and turned into great new products like Method Bins Method Recycling | Office Recycling Bins Made Beautiful NZ. Thanks to a new optical sorter at Visy recycling in Auckland, they now separate out PP as its own recycling stream and send if off to Astron to reprocess it to be used by manufacturers locally.
- Pharmapac have partnered with Future Post (winners of the top Agricultural Innovation award) who recycle a portion of their post-industrial recycling. Future Post was built on kiwi ingenuity and the brain child of Jerome Wenzlick, recycling plastic and turning it into fence posts. See more here: futurepost.co.nz
Why we don’t use Compostable or Biodegradable plastic bottles:
- We took into consideration Pharmapac’s research as follows:
-
At Pharmapac we have chosen recyclable polymers over alternatives such as compostable or biodegradable plastic bottles. Based on the research we’ve done, and feedback from our clients and industry organisations, recycling has been shown to be the most efficient way to make a difference today.
At present there are no suitable options for at scale mainstream processing of compostable or biodegradable bottles, so when they are sent to landfill or are mixed in with recyclable bottles, they can actually cause more problems. While great in concept, there is still a lot of confusion in this area as far as what will break down in home compost environments vs commercial composting facilities (NZ has limited commercial composting facilities) and the effect biodegradables have on landfill environments.
For all of these reasons, we’ve chosen to promote recyclable packaging while we keep up with the research and keep an eye on advancements in this area.
We have also designed in features to our packaging with end recyclability in mind. For example, our removable tamper evident band on our packaging allows separation of dissimilar resins during the recycling process
- HDPE and PP is used worldwide and many companies are partnering with their local recycling business to meet sustainable and environmental goals. The messaging in New Zealand is choosing packaging made from polymers 1, 2 and 5.
Pharmapac HDPE containers:
- Fully tamper-evident
- All materials used meet with FDA and EU 10/2011 standards
- Lightweight packaging alternatives – on average 7x lighter than its glass counterpart – minimising environmental footprint in product and shipping.
Pharmapac PP Polypropylene closures:
- Stiffer than HDPE, polypropylene provides greater resistance to fatigue (the main cause of seal failure from backing off or creep, resulting in less wastage from spoiled goods).
- Good moisture vapour barrier - (Low permeability
to water vapour) making it 6.5 - 8.5 times more moisture resistant than alternative PET packaging - Fully tamper-evident
- Pharmapac bottles are on average 7 x lighter than glass counterpart – minimising environmental footprint in production and shipping
Our goal is to be an environmentally friendly brand. We’re learning there are many different factors we have to consider as we strive to meet this goal.